TRANSFORMER OIL REGENERATION PLANT CMM-R12
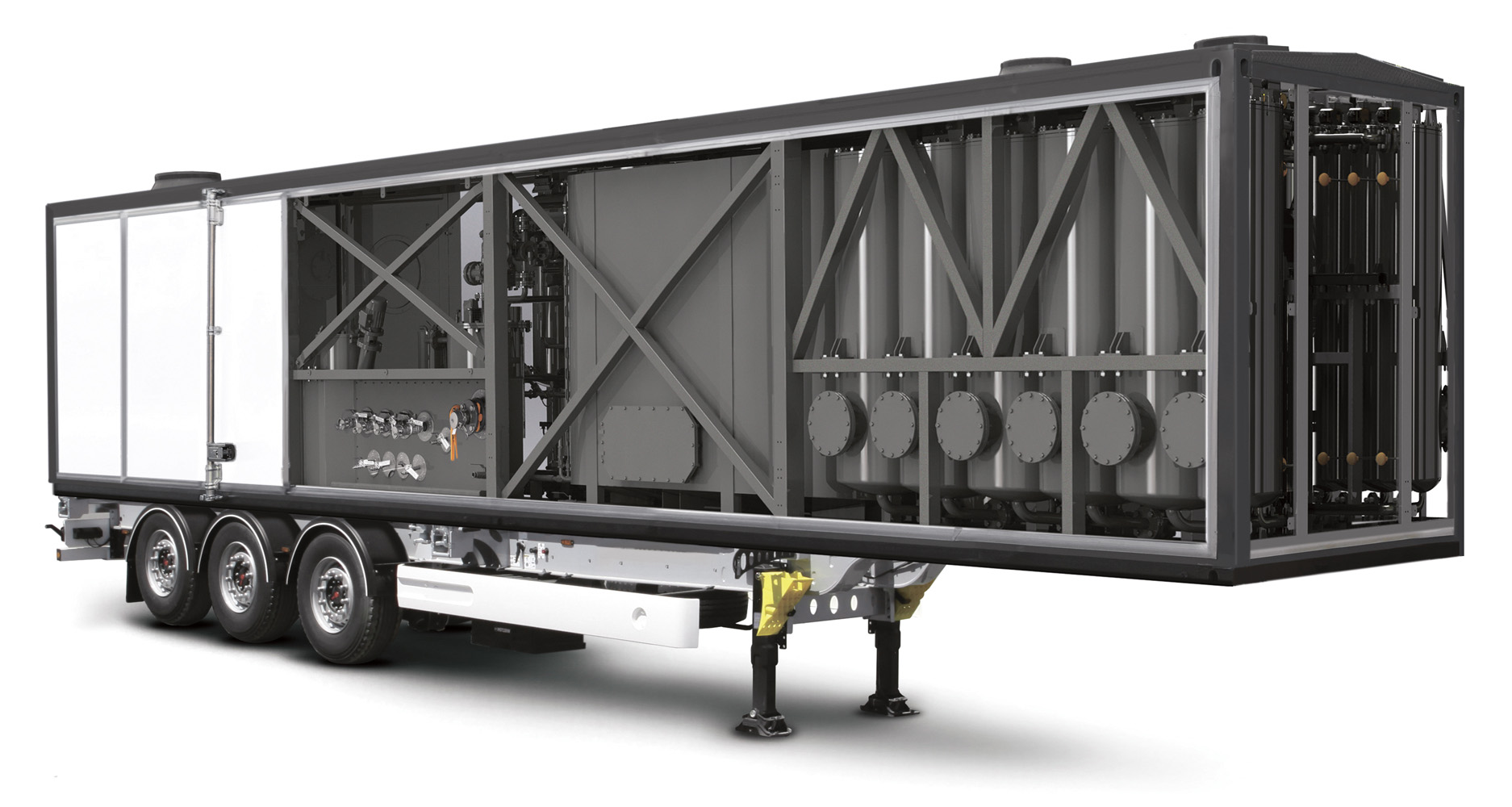
СММ-R12 Transformer Oil Regeneration Plant
Design and Operation
The unit comes in several configuration options:
- stationary
- mobile on trailer
- with degasser and operator compartment
- with auxiliary regeneration module
Technical Specification
Parameter | Unit | Value |
Capacity | liters/hour | 4000 |
Oil lost during regeneration | % | 2-20 |
Max allowable oil temperature | оС | 80 |
Outlet pressure | bar | 2,5 |
Oil heater power | kW | 75 |
Nominal suction rate of the vacuum system | liters/hour | 280 000 |
Filler’s earth load | Kg | 1600 |
Max power consumption, with/without the CMM-R12D auxiliary module | kW | 130/145 |
Power | ||
Phases | 3p+1N+PE | |
Voltage | V | 380 |
AC frequency | Hz | 50 |
Connections | ||
Oil in | Dn | 40/Camlock C150 |
Oil out | Dn | 40/Camlock C150 |
Vacuum pump exhaust | Dn | 32 |
Reactivation exhaust | Dn | 50 |
Filter elements | ||
Coarse filter (mesh strainer) | micron | 100 |
Pre-filter with filtering element | micron | 25 |
Regeneration section filter with filtering element | micron | 0,3 Х 2 |
Fine filter with filtering element | micron | 5 |
Dimensions (no trailer) | ||
Length | mm | 11500 |
Width | mm | 2090 |
Height | mm | 2110 |
Weight | kg | 15000 |
New processed oil parameters
Parameter | Unit | Value |
Per 1 vacuum/heat degassing cycle | ||
Moisture by weight | g/t | 5 |
Gas content by volume | vol % | 0,1 |
Per 3 vacuum/heat degassing cycles | ||
Moisture by weight | g/t | 3 |
Gas content by volume | vol % | 0,05 |
Parameters of used oil after regeneration
Parameter | Unit | Value |
Per 1 vacuum/heat degassing cycle | ||
Moisture by weight | g/t | 5 |
Gas content by volume | vol % | 0,1 |
Acid number, IEC 296; ASTM D-664 | mg KOH/g | 0,01 |
Corrosive sulfur, ISO 5662; ASTM D-1275 | None | |
Dielectric strength, IEC 156; ASTM D-1816 | kV | 70 |
Interfacial tension, at 25ºС, ISO 6295; ASTM D-2285 | N/m | 45 |
Dissipation factor at 90ºС, IEC 247; ASTM D-924 | 0,01 |
Attention! Oil parameters may vary. Processed oil parameters depend on original oil condition.
The GlobeCore regeneration process restores used oils to new like condition. This process makes it possible to fill transformers with oil that would previously require disposal. The oil in the transformer can be used without replacement for the entire service life of the transformer.
The GlobeCore CMM-R systems are designed to extend transformer service life by restoring the dielectric strength and chemical composition of dielectric insulating oil.
In the process of oil regeneration, oil degradation products and acidic compounds are removed, the oil becomes clear, oxidation resistance is improved, while gas solubility is reduced.
This equipment allows to reduce acid number of transformer oil to the regulated values. A special feature of the process is the reduction of soluble and insoluble sediment. This sediment is harmful in that it deposits in the cellulose insulation, being much more acidic than the oil. The oil has a tendency to precipitate acidic products which then concentrate in the paper insulation. The acidity of the oil then changes very slowly. Further growth of oil acidity accelerates and is accompanied by formation of insoluble sediment and water-soluble acids.
Each GlobeCore unit can be customized and includes a number of options:
- An extra vacuum pump assembly for transformer vacuuming
- Mounted on a trailer or a semi-trailer
- Inlet and/or outlet moisture meters for the oil stream
- Remote control and process monitoring via smart phone or PC
- Climate Controlled Operator work room
СММ-R12 Specifications
Configuration of equipment
Component | Description | Note | ||
Number of sorbent column/ recommended matching degasser | 12/4000 | 1600 kg Fuller’s earth load / 4000 liters/hour degasser | ||
Oil inhibition section | The system adds DBPC additive to the oil | |||
AC power voltage | 380V, 3 phases | |||
AC frequency | 50 Hz | |||
Ambient temperature range | +5…+40oC | |||
Sockets for additional equipment (specify amount, type and current) | 3ph 32А | 1 | ||
220 10А | 3 | |||
Programmable Logic Controller
(PLC) |
Manages oil processing | |||
Laptop controls | Displays process diagram and facilitates control of the plant by keyboard and mouse input | |||
GSM module | Remote monitoring of plant operation | |||
Printer | Plant operation data output | |||
Digital oil meter | Measures the amount of processed oil. This can also measure the current flow rate through the plant | |||
Moisture content meter | Measures the amount of moisture in the oil | |||
Oil inlet | Dn40 | L -30 meters | ||
Oil outlet | Dn40 | L -30 meters | ||
TSS (Transformer Security Sestem) | Monitors oil level in the transformer. If the transformer oil level drops below critical level, the plant stops | |||
Metal container | The unit is installed in a metal container with a metal roof and detachable doors for servicing | |||
Operator compartment | The unit comes with a compartment for the operator. The compartment is equipped with a desk and air conditioning | |||
Charcoal filter + catalytic converter | Reduces the amount of harmful substances in the exhaust. Provides maximum environmental protection. The filtering element must be changed from time to time | |||
Adaptor kit for transformer connections (specify diameter range) | Connects the plant to various transformers
0.¾” – 2” |
|||
Soft throughput control (PID) | Allows automatic processing rate control | |||
Soft heating control (PID) | Allows gradual oil temperature increase and keeping the temperature by varying the current | |||
Auxiliary regeneration module capability | Plant software and hardware are prepared for connection of up to two auxiliary 12 column regeneration modules |
SCOPE OF APPLICATION
The unit is designed for regeneration of mineral transformer oil.
Oil ages in the course of long operation. The products of oil aging are various chemicals with harmful influence on both the oil’s performance as a dielectric and on the functions of electrical systems. The solution to this problem is periodic oil regeneration.
The unit is designed for use during installation, operation repairs and maintenance of high voltage oil filled equipment (power transformers, high voltage switches etc).
The unit can process electrical insulation oil and service transformers.
Electrical insulation oil processing includes:
- Removal of solved gases
- Removal of free and solved water
- Removal of particulate matter
- Removal of oil degradation products
Transformer servicing includes:
- Vacuumizing the transformer
- Heating of the transformer and its core with hot oil
Removal of sediment form the windings of the transformer
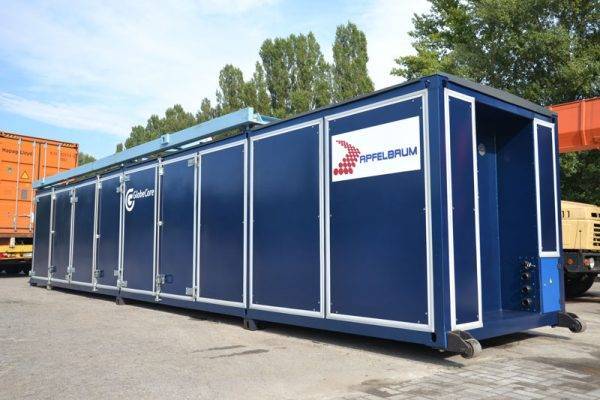
CMM-12R unit before shipment
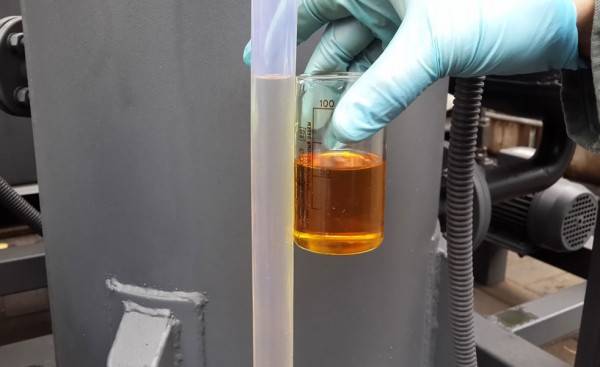
The oil before regeneration is in the glass vessel, regenerated oil is in the sight tube