The bottlenecks in production of rubber and latex articles are long desintegration and mixing time, difficulty of uniform distribution of extenders and other ingredients into the caoutchouc and latex, long vulcanization time.
To activate particle surface of extender (for example, soot) it can be exposed to the grinding by ball or vibrating mills. But this processing way is labour-intensive and gives marginal effect. Most effective way is chemical modification of the extender.
One of the ways of kaolin chemical modification is based on the common sedimentation of kaolin and calcium silicate suspension. In this case calcium silicate is generated during the blending of sodium silicate solution with calcium chloride.
It was investigated that kaolin surface activation in AVS unit leads to increasing of the durability of rubber-based vulcanizate to 84,3%.
Modification of the extender leads to increasing of durability of the vulcanizate. It can be explained by creation of adsorbed layer of modifying agent on the kaolin particle surface which helps to adsorption and chemical bond formation between the particles of extender and caoutchouc’s molecules.
We have investigated that by using AVS unit (table 1) kaolin surface activation leads to increasing of the durability of rubber-based vulcanizate to 84,3%. At the same time other characteristics are not changed. The best results were obtained when we treated the kaolin by vortex layer from 1 to 5 minutes.
Table 1
Rubber tensile strength, obtained on the base of rubber SKS-30 AKRP-N filled by activated kaolin (σр·10-5 Pа*)
Cure time under 143ºС, min |
Kaolin activation time by AVS-100, min |
Kaolin activation time by ball mill, min |
||||||
0 |
1 | 2 | 3 | 4 | 30 | 60 |
120 |
|
20 |
2,9 | 39,3 | 3,9 | — | — | — | — |
— |
30 |
9,81 | 22,6 | 24,5 | 73,6 | 6,57 | 9,8 | 45,1 | 43,2 |
40 | 21,6 | 32,4 | 41,2 | 92,2 | 86,3 | 21,6 | 65,7 |
64,7 |
60 |
62,8 | 58,9 | 57,9 | 116,0 | 105,0 | 63,8 | 47,1 | 51,0 |
80 | 55,0 | 50,0 | 76,6 | 92,2 | 55,0 | 29,4 | 29,4 |
55,0 |
* Specific elongation and residual elongation, vulcanization rigidity were not changed
Chalk processing for 10 minutes by means of vortex later leads to increasing of structural behaviours to 51,5% (table 2). At the same time chalk processing by ball mill has no effects on the durability of the vulcanizate. Increasing of rubber`s durability filled by extenders activated in AVS is reached by means of growing of adsorptive capacity of these extenders.
It was established that by using AVS unit for kaolin processing its adsorptive capacity can be increased in 2-3 times.
Table 2
Rubber tensile strength, obtained on the base of rubber
SKS-30 AKRP-N filled by activated chalk (σр·10-5 Pа*)
Cure time under 143ºС, min |
Chalk activation time by AVS-100, min |
Chalk activation time by ball mill, min |
||||||||
0 |
1 | 2 | 3 | 5 | 10 | 20 | 3 | 60 | 120 | |
30 | — | 34,3 | 26,5 | 29,4 | 30,4 | 25,5 | 25,5 | — | — |
— |
40 |
32,4 | 33,3 | 30,4 | 32,4 | 43,2 | 49,0 | 36,6 | 33,3 | 33,3 | 40,2 |
60 | 35,3 | 22,6 | 29,4 | 29,4 | 29,4 | 44,1 | 29,4 | 25,3 | 32,4 |
38,3 |
80 |
27,5 | 27,5 | 22,6 | 30,4 | 34,3 | 36,3 | 35,3 | 21,5 | 28,5 |
30,4 |
From 1 to 10 minutes of treatment has continued directly-proportional dependence: adsorption capacity of kaolin increases proportional to the time of processing by AVS. Adsorption amount depends from the balance between solid and liquid phases, value of magnetic induction in the working chamber of AVS unit, form and size of ferromagnetic particles, density of vortex layer.
Adsorption capacity of kaolin increases proportional to the time of processing by AVS
Extremely strong change of extender’s adsorption capacity permits to apply AVS unit for chemical modification of kaolin and chalk.
Filling of caoutchouc by kaolin modified at the vortex layer by means of one of universal inhibitor (DMBA) leads to cure rate increasing in 5-8 times and vulcanizate durability increasing in 2 times.
Possibility of dry powders chemical modification is the one of the particularities of AVS unit application. Effect of rubber reinforcement and applying such extenders depends from the processing time and operational conditions of the vortex layer.
In the rubber production process by using latex the most volume of expenditures are paid for preparation of ingredient`s dispersion, curing agent dispersion, kaolin and soot, etc. On our and foreign plants these dispersions are prepared by using ball and vibration mills. In this case grinding duration can reached 70 hours or even more.
Application of AVS unit intensifies the process of suspension production and allows increasing the quality of products.
Table 3
Comparative data of sodium fluate stability
obtained by using AVS and ball mill
Suspension preparation time |
Maximum particles size, mcm | Daily settle, % | |
by AVS, seconds |
by Ball mill, hours |
||
10 |
— | 3 | 35 |
20 | — | 2 |
34 |
30 |
— | 1 | 27 |
60 | — | 1 |
26 |
— | 48 | 5 |
100 |
This table shows that by using AVS can be obtained fine and stable suspension of sodium fluate. In this case time of preparation can be reduced in 1700 times.
Our technology is implemented by different factories to produce suspension of latex technology. Productivity of this unit is 1 m3/h (fig. 1). Application of AVS units give a possibility to replace 8 vibration mills (each of these mill has a volume 400 liters), and in addition implement to the uninterrupted process which allow increasing the quality of manufactured product.
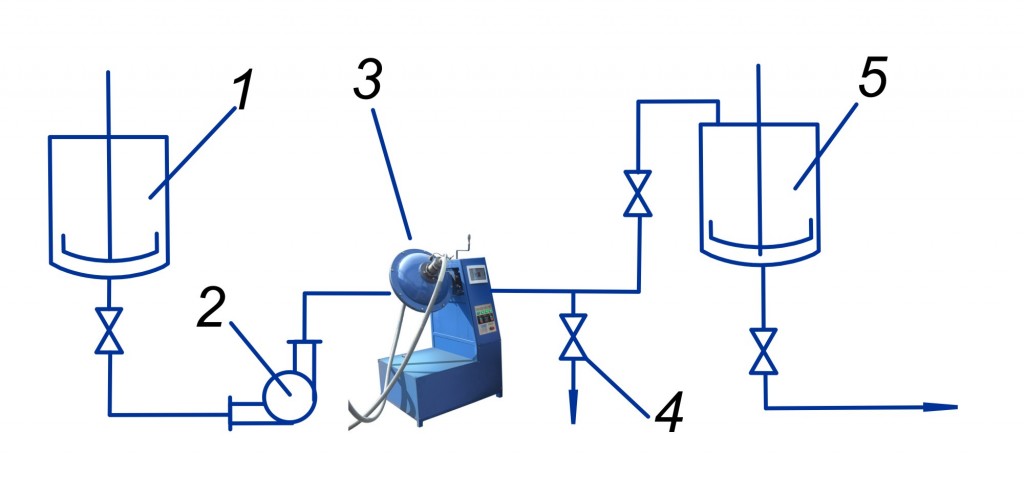
Figure 1. Application of AVS unit. Suspension production technological diagram
1 – vessels for pre-mixing of components; 2 – pump; 3 – AVS; 4 – valve for sampling; 5- tank for prepared suspension
Table 4
Comparative data of latex sponge physical and mechanical properties
The mode of vulcanizator’s general dispersion preparation |
Physical and mechanical properties of the latex foam | |||||
volume weight, gr/cm3 |
Hardness НВ·10-5, Pа |
Breaking strengthσр·10-5 Pа | Stretch ratio, % | Elastic recovery, % |
Residual deformation after repeated compression, % |
|
Ball mill |
0,102 |
0,198 | 0,338 | 137 | 88 | 19 |
0,119 | 0,173 | 0,322 | 133 | 89 |
28 |
|
0,106 |
0,154 | 0,326 | 108 | 91 | 25 | |
0,126 | 0,204 | 0,334 | 126 | 91 |
15 |
|
AVS |
0,099 |
0,097 | 0,400 | 176 | 90 | 1,2 |
0,101 | 0,091 | 0,401 | 180 | 90 |
0,9 |
|
0,101 |
0,098 | 0,407 | 180 | 98 | 1,2 | |
0,101 | 0,098 | 0,407 | 180 | 98 |
1,2 |
By using AVS we can obtain such mixtures of kaolin and natural latex (parotex) which is antifloating during 2 weeks.
All prepared in AVS suspensions are very stable and antifloating. After 5 min mixing in AVS unit we obtain suspension which separate during the day only in 5 %. The same suspension but obtained by using ball mill (processing time – 4 hours), is separating during the day in 100%.
The carbon black suspension prepared by AVS is antifloating. At the same time, the same suspension prepared in ball mill is unstable and after one day is completely separated.
The efficiency of AVS unit on latex production is obvious.
If you don’t found on this website the information you need concerning application of AVS unit, you can contact directly with the manager in charge of AVS unit by using only following email: [email protected] or skype: mg5globecore_de and we will prepare for you all required information as soon as possible