Regeneration of transformer oil at the transformer’s location is an important preventive measure of transformer servicing.
Transformer life time is, in essence, the life time of its insulation system. The most widely used insulation is liquid insulation (transformer oils) and solid insulation (paper, i.e. cellulose insulation). The oil provides for at least 80% of the electric strength in a transformer. Almost 85% of transformer failures are caused by damaged insulation.
Transformer oil is a good insulator when insulation paper is will impregnated: the oil increases the breakdown voltage of the insulation which it saturates. Low viscosity of the oil allows it to permeate solid insulation and dissipate heat by transferring it to the cooling system. Therefore, liquid insulation is also a cooling liquid. Oxidation stability of the oil allows it to endure high temperatures and prevent significant damage to the insulation system.
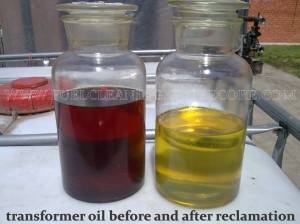
Aging or degradation of transformer oil is usually related to oxidation. As oxygen and water appear in the oil, the oil oxidizes even of other conditions are perfect. Contaminants generated by solid insulations also affect the quality of transformer oil. Reactions which occur in the oil between unstable hydrocarbons, oxygen and other catalyst, such as moisture, with such accelerators as heat, lead to oil decomposition (oxidation).
Heat and moisture, along with oxidation, act as primary accelerators of this process and are the largest threat to solid insulation. If the cooling and insulation system is serviced right, insulation system’s life time can be extended from 40 to 60 years. Unfortunately, oil oxidation cannot be entirely eliminated, however, it can be controlled and slowed by oil treatment. One of the most important transformer maintenance procedures is oil analysis scheduled at least annually. Oil analysis is indicative of the overall insulation condition.
Moisture is a combination of free water, water solved in the products of oil degradation, solved and chemically bound water (it is a part of glucose molecules and is necessary for maintaining the mechanical strength of cellulose). It is impossible to completely dehydrate cellulose insulation.
Transformer oil solves more water at higher temperatures. If the mixture of oil and water is cooled, water will settle out of the oil. The oil will permeate solid insulation, or become bound to oil degradation products. Moisture will distribute itself between the oil and the paper. However, this distribution will be uneven: paper absorbs water from the oil and retains it, in the areas of highest voltage.
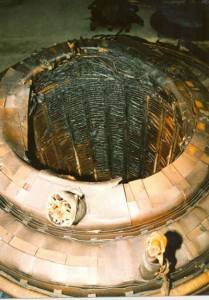
Damage to inside of coil winding stack of oil filled transformer
Contaminants are formed in the process of transformer operation. Oil decay products are acidic, and they attack cellulose and metals; the acids also create soaps, aldehyde and alcohol, which settle on the insulation, tank walls, breathing and cooling systems in the form of sludge. Sludge forms faster in a heavily loaded, hot transformer operated incorrectly. Sludge increases oil viscosity thus reducing its cooling ability, which has further negative effect on transformer life time.
Contamination also causes insulation to shrink, destroys varnish and cellulose material. It is a conductor for discharges and currents; being hygroscopic, it absorbs moisture and leads to insulation overheating. Sediment forms on the core, which increases transformer temperature.
Cellulose material is the weakest link in the insulation system. Since transformer life time is in essence the life time of its cellulose insulation, and since cellulose degradation is irreversible, contaminants must be removed immediately, until they damage the cellulose. A good maintenance program extends its life time significantly.
Normal servicing of power transformer should attain a practical life time of 50 – 75 years. However, the actual condition of insulation defines the difference of real time operation between 20 – 50 years plus the transformer life time. Experience shows that the most common cause for transformer failure is inadequate servicing and incorrect operation.
Transformer oil can be completely regenerated and made as good as new. Insulation oil can be used indefinitely, if it is processed regularly. The prospect of regenerating a batch of very poor quality oil should be balanced against the relatively high cost of acquiring new oil.
Removal of water and keeping the insulation dry is of utmost importance. Moisture accelerates aging. 1% of moisture in cellulose accelerates aging by one order of magnitude in comparison to 0.1% moisture content.
So, what are the main guidelines for preventive maintenance?
Purification of transformer oil, including regeneration, is a method of extending transformer life time.
The objective of this process is to remove aging product from solid insulation and oil before they damage the insulation system (insulation damage may be determined by furan compounds).
A well planned maintenance strategy aims to avoid accumulation of moisture in insulation and make sure that the transformer always operates in a clean environment.
To stop or slow the aging process of transformer insulation, the oil must be kept in the best possible condition. The following measures will help:
- Constant control of oil condition;
- Silica gel in the breather must be in good condition (blue). Never allow more than one third of the silica gel volume to change color to pink;
- Repair oil leaks as soon as one is detected;
- Start using an oil purification system for dehydration of oil to 10 ppm at most;
- Do not add oil contaminated with moisture (if the oil was kept in an open vessel);
- Start drying the oil as soon as moisture content exceeds 20 ppm or the breakdown voltage drops to below 50 kV;
- Keep a close eye on the oil’s acidity and regenerate the oil when it reaches the critical level of 0.2 mg KOH/g. Best use a Fuller’s earth system with renewable sorbent (Globecore CMM-R is a good choice);
Sometimes oil should be changed (filtered, rinsed, and refilled). This procedure is best performed on site. Oil is drained form the transformer. The interior of transformer tank is rinsed with hot naphthene or regenerated oil to remove sediment concentrations; then the transformer is filled with regenerated oil.
If the transformer is rinsed only through inspection opening, only approximately 10% of the interior surface will be cleaned. In this case, a film of contaminated oil remains on most of the winding surface and the tank’s interior. Keep in mind that up to 10% of the oil in the transformer permeates cellulose insulation. The oil remaining in the insulation and the transformer contains polarized structures and can poison a large amount of new or regenerated oil.
If the top lid is removed for rinsing, approximately 60% of the interior can be cleaned. Better results can be achieved by using a Fuller’s earth regeneration system, such as GlobeCore’s CMM-R, on a live transformer.
A simple replacement of oil does not remove all sediment, which accumulates in the cooling system and between the windings. This sediment will dissolve in new oil and cause oxidation.
How to regenerate and remove contamination on site
Oil may be regenerated directly in working transformer (prior analysis indicates if such possibility exists, especially the DGA test). The oil is pumped from the tank’s lower valve to the regeneration system, where it is purified, regenerated and degassed before going back to the transformer through the transformer expansion tank. The process continues until the oil is restored and complies with standards or other specifications. If CMM-R unit is used, hot oil is regenerated by percolation through fuller’s earth, then filtration and vacuum degassing and dehydration.
The difference between regeneration and purification is that regular purification cannot remove such things as acids, aldehydes, cetones etc, solved in the oil. Therefore, simple purification cannot change the oil color from dark to light clear yellow. Regeneration, however, incorporates filtration and dehydration.
When regenerating oil, the following results may be expected:
- Moisture content less than 10 ppm;
- Acidity below 0.02 mg KOH/g oil;
- Breakdown voltage of at least 70 kV;
- IFT at least 40 dynes/cm;
- Tan delta less than 0.003;
- Contaminants solved or suspended in the oil are removed;
- Oxidation stability restored;
- Oil color changed to clear light yellow;
- Solid insulation breakdown voltage improved.
Despite the removal of solved or suspended solid contaminants, regular regeneration cannot remove sediment. It is necessary to remove sediment if acidity of the oil is above 0.15 mg KOH/g and IFT is less than 24 dynes/cm. Sludge removal involves circulating hot oil through the transformer. The oil is heated to the point when it becomes a solvent for the sludge. If the transformer is operating, vibrations of the windings enhance the process.
Next to consider is shrinking of insulation and dehydration of transformer oil.
Solid insulation may shrink as a result of motion of loaded coil, specifically, under shock loads; shrinking may become a source of premature failure. Shrinking also comes as a result of cellulose degradation. On-site regeneration of transformer oil does not cause insulation shrinking.
Experience shows that if the transformer insulation is super-dry (up to +2% of dry weight), shrinking does not occur. The regeneration process does not aim to dry transformer insulation. It is impossible to dry the insulation within the time of regeneration. High level of dehydration requires significant time.
Moving moisture from insulation by thermal diffusion is a natural process of restoring the balance between the winding insulation and the oil. The process rate depends on the level of water diffusion through solid insulation.
Removal of sediment from transformer core
Insulation forms and accumulates in cellulose fibers. During purification, the oil is heated to the point when sediment becomes soluble in oil. The process guarantees that the solved contaminants will be removed by regeneration and oil will become clean.
Obviously, regeneration and purification is broader than simple oil restoration.
Loss of furan values
Restoration (regeneration or purification) or replacement of transformer oil destroys furan compounds, which are used to measure the degree of polymerization (insulation condition and life time). Furan analysis should be done before the process.
If transformer oil is allowed to degrade beyond salvaging without regeneration or purification, transformer life time decreases significantly. After purification, a new base line for furan compounds control is established. Future furan test must be referenced against this new base line.
Removal of aromatic compounds
Some types of aromatic compounds may have anti-oxidation properties. Most specifications require that the content of polyaromatic hydrocarbonate be equal or less than 3%. Too much aromatic compounds reduce dielectric or impulse strength and imcrease the oil’s ability to solve most of the solid insulation submerged in oil. Oxidation stability of regenerated oil (after 164 hours at 100 degrees C) was 0.006% by weight, which is lower than the highest allowable level of 0.1% by weight.
Before regeneration is started, the whole system, including the hoses, is filled with oil. Old oil and suspended contaminants accumulated in the bottom of the transformer tank are removed from the lower part of the tank. Regenerated, filtered and pure oil enters the transformer via the expansion tank above. This is done to ensure the level of oil in the transformer is unchanged. The oil freely circulates and the contaminants do not reenter the tank. Only the clean, dehydrated, degassed oil returns to the transformer.
Regeneration is a consistent, somewhat slow process, which solves and removes contaminants from the transformer.
It is important to use only automatic oil heating to keep the oil temperature within limits so as to avoid thermal oxidation and destruction of oil. Using a well designed machine makes the process of transformer oil regeneration safe and economical. However, equipment of lower quality may damage the oil by overheating.
What happens after regeneration
If insulation contains moisture, the level of moisture content on the oil is expected to increase. Moisture will move from insulation to the oil to restore the balance of operation temperature between cellulose and oil. Dielectric strength will fall somewhat with increase of oil moisture content.
If a significant increase of acidity is observed within a short time after regeneration, this is caused by solution of contaminants. This means that the result of regeneration is largely dependant on how long the process takes. Low quality regeneration systems may damage the oil and reduce its oxidation stability, therefore accelerating oil degradation.
Quality of properly regenerated oil is guaranteed for at least two years with consequent purification, if the transformer is well sealed, breather valve and silica gel are serviced in a timely manner, and transformer is operated correctly in terms of load and temperature. A lot depends on the initial quality of oil, insulation type and the environment.
Final testing of the oil after regeneration should include gas and moisture content analysis and breakdown voltage test.
Recommended transformer oil procedures
Regeneration of oil inside or outside of the transformer, while it the transformer is on or off, depends not only on technical parameters, such as gas content etc, but also on economic considerations.
Regeneration is an important part of transformer servicing and should be completed before the oil reaches a critical stage, which may damage solid insulation. If the transformer oil is processed in a timely manner, accumulation of moisture and sludge in solid insulation will be negligible.
Older transformers with very poor quality of oil and insulation (40 years and older) with due point (polymerization degree) below 210, may still be successfully treated while they still operate.
After first regeneration, the transformer will operate well for 5 to 8 yeas. Regular maintenance ensures that in the long run the transformer will only require annual oil test and occasional oil treatment by regeneration.