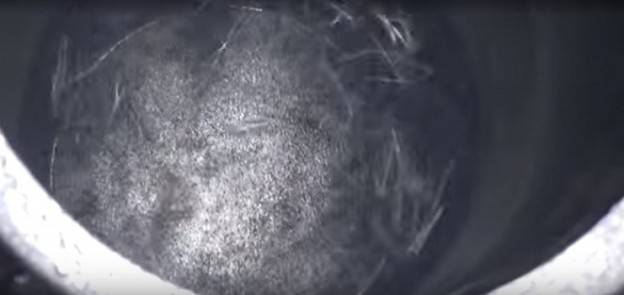
Electromagnetic devices with a vortex layer of ferromagnetic particles were first proposed in the 1960s. In these devices, complex interactions take place between ferromagnetic particles, fluids and materials that are being processed. This speeds up the process of mixing and grinding. Moreover, the vortex layer devices can successfully be used as reactors.
GlobeCore manufactures the AVS-100 and AVS-150 type vortex layer devices. These units are highly versatile pieces of equipment that can be used for the following:
- production of bone food paste;
- production of mayonnaise;
- processing vegetable raw materials;
- cleaning vegetable oils;
- intensification of the technological processes of bakery production;
- cleaning wastewaters by removing chromium and other heavy metals;
- production of biodiesel;
- preparation of water-fuel emulsions; and
- disinfection of liquid pig manure.
The effect of grinding the treated raw material depends on the nature of the movement of the ferromagnetic particles in the work chamber of the unit. Grinding can be achieved by both free collision of the particles with the ferromagnetic elements and through a constrained collision between the two elements or elements and the housing.
During operation of the vortex layer devices, gradual abrasion of the ferromagnetic particles takes place. This can lead to a decrease of their quantity and deterioration of the quality of processing of the feedstock. During the technological process therefore, it is necessary to maintain the optimum amount of the ferromagnetic particles in the processing chamber. This should be carried out in a continuous mode. The stoppage of the production line every time the number of ferromagnetic elements falls below a critical level, in most cases, is simply not possible from the technical standpoint.
GlobeCore has developed and manufactures special devices that measure the amount of the ferromagnetic particles in the work chamber of the vortex layer devices. In the case of critical values, the special devices are able to make the addition of new ones. The optimal amount of the ferromagnetic elements for each technological process will vary, hence their critical amount will be different respectively. The amount can be set on the control panel of the equipment.
Besides the production of vortex layer devices, GlobeCore also provides delivery for its work chambers and ferromagnetic particles in all corners of the globe.