Fluorine-containing wastewater
The wastewater from chemical and metallurgical enterprises which contain fluorine compounds is classified as harmful wastewater. Treatment of these wastewater from fluorine involves some problems and requires of considerable expenses and expensive reagents.
Water treatment from slight fluorine concentration is extremely important. These difficulties are concerned with chemical particularities of fluorine compounds. As is well-known, the substantial dissolubility has only alkali metal salts of fluoride, potassium, and ammonium.
Regardless of the fact that all metal fluorides (except for alkali metal fluoride) named as “marginally soluble” or “insoluble”, their solubility exceed the acceptable sanitary regulation for fluorine content in water in tens of times.
Enterprises encounter with formidable difficulties during the treatment of wastewater from fluorine. For example, acidic water from superphosphate production plants contains up to 2,5 g/l of fluorine. The chalk or lime milk is usually used for wastewater neutralization and fluorine elimination. The water is treats by the chalk (lime milk) in the 40 m3 reactor-neutralizers which are equip by arm mixers. Hardly soluble substances such as CaF2, CaSO4, CaHPO4, Ca3(PO4)2 are precipitated in the result of chemical transformation.
Methods of wastewater treatment from fluorine
Usually enterprises are used two methods of fluorine-containing wastewater treatment:
- Chemical method by using different reagents;
- Sorption method
As reagents in the chemical method of wastewater treatment can be used lime, calcium salt, magnesium salt, lead salt, basic ammonia chloride and others.
It was observed that application of AVS unit for fluorine-containing wastewater treatment is more effective than current used equipment
Compared to other salts which can be used as a reagent, the calcium salt has more advantages. Application of calcium salt allows creating of highly coagulable sediments.
Neutralizing product (calcium fluoride) can be used as commercial product. This product is comparative marginally soluble (dissolubility is 15,6 mg/dm3)
The most effective fluorine ions precipitating agent is technological lime. Active calcium oxide containing in the lime has a significant importance. Other chemical precipitating agents leave a great quantity of its in treated wastewater.
It is established that the presence of HCO–3 and SO2-4 ions in wastewater is the cause of increasing of CaF2 sedimentation speed. To the contrary, the presence of fluorine ions in the water is the cause of decreasing of CaF2 sedimentation. Therefore it should be noted that it is impossible to well purify the wastewater from fluorine by use only reagents whose action is focused only on chemical reaction of sedimentation.
The sorption method of wastewater treatment is based on utilization of different sorbents which are acting under the chemisorption principle.
Let us look at the following wastewater characteristic and description of the technological schema of wastewater treatment of superphosphate production (chemical method of treatment is used). The wastewater contain not less than 1500 mg/dm3 of fluorine, not less than 6500 mg/dm3 of phosphates, pH is on level 2,5-3,5.
Chalk and lime is wide used by enterprises as a reagent for neutralization and treatment of fluorine-containing wastewater. Hardly soluble and insoluble compounds such as CaF2, CaHPO4, Ca3(PO4)2, SiO2 are precipitate in the result of chemical transformations
Traditional used method of treatment from fluorine
Neutralization and treatment of fluorine-containing wastewater is made in the following way.
Pre-treatment of fluorine-containing wastewater begin in the lime-slaking apparatus in which prepare the lime milk with 1-3% active CaO content.
Installation of the AVS-100 unit enables one to provide a treatment quality below the maximum permissible concentration, reduces the consumption of reagent by 1.5-2 times, the consumption of energy by 2 times, reduces the working area by 10-15%, which results in high economic benefits
Partially defluorinated wastes with pH level 10-13 are entered in the intermediate container and then by natural flow are entered to reactors. Further treatment is carried out in the chain of reactors
Neutralized and defluorinated wastewater are entered in clarifier. The wastewater settles out in that clarifier basin. Residual fluorine content in sterilized wastewater is 50-60 mg/dm3, pH 8-12, calcium content is 2500-6000 mg/dm3. Sterilization time in reactors is 30 min.
It was investigated that if we use the chalk as a reagent for fluorine-containing wastewater treatment, we obtain the residual fluorine content in the water in 1,5-3 times and phosphate ions in 10-20 times more than if we use the lime milk. In this level of treatment we cannot discharge the defluorinated wastewater into water supply sources. Fluorine content cannot exceed 1,5-60 mg/dm3.
Application of AVS unit for fluorine-containing wastewater treatment
In this investigation we have used
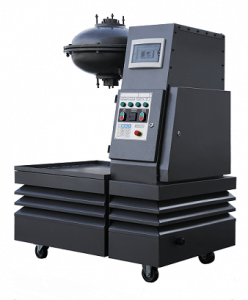
- wastewater with fluorines content 1375 mg/dm3,
- phosphates – 4500 mg/dm3,
- water pH – 3.3,
- 10% concentration lime milk,
- processing time in the AVS unit – 1-30 seconds,
- reagent consumption – 70-120% from stoichiometric,
- pH of defluorinatation process – 4-12.
Results of investigations are on the table 1
Table 1
Fluorine content in wastewater after treatment by AVS unit, mg/dm3
Lime milk consumption (active CaO), %
|
Processing time, s |
1 |
3 |
5 |
10 |
20 |
30
|
70 % fromstoichiometric calculation
|
90,00 |
88,0 |
86,0 |
84,0 |
82,0 |
80,0 |
90 % fromstoichiometric calculation
|
42,0 |
40,0 |
38,5 |
36,5 |
34,6 |
33,0 |
stoichiometric calculation |
30,0 |
29,0 |
25,0 |
23,5 |
19,0 |
17,0
|
110 % fromstoichiometric calculation
|
20 |
15 |
12 |
9 |
6,0 |
2,0
|
As is known, pH of the medium has a considerable influence on the wastewater treatment process. Optimum pH of the medium leads to the optimal treatment results.
For this investigation we have used the wastewater with following content: fluorine – 1375 mg/dm3; phosphates – 4500 mg/dm3. During the treatment process we changed the wastewater pH from 4 to 12.25 by using 10% lime milk. Processing time is 1-3 seconds.
Results of investigations are on the table 2
Table 2
The pH influence on the effectiveness of wastewater treatment after processing by AVS unit
Residual content, mg/dm3 |
pH ofwastewater
|
4 |
5 |
5,7 |
6,35 |
7,0 |
8,1 |
9,2 |
10,1 |
11,0 |
11,9 |
12,25
|
F
|
180,0 |
92,0 |
65,0 |
55,0 |
45,0 |
25,0 |
15,0 |
11,0 |
7,0 |
3,9 |
1,35
|
P2O5 |
1920,0 |
720,0 |
450,0 |
83,5 |
27,0 |
0,2 |
0 |
0 |
0 |
0 |
0
|
We have made our investigations in industrial conditions by using industrial installation of AVS unit. According to our technological schema, untreated waste from industrial shopfloor enters to the equalizing tank; lime milk (prepared in the lime carbonater extinguisher) enters into consumption tank.
Equalized waste and lime milk uninterruptedly enter the AVS unit by means of dosing pump. All these components are mixed (also take place dispergation and electromagnetic processing) and are entered to the settling tank for further defecation. Flow meters are controlling the consumption of wastewater and lime milk, pH of wastewater are controlling by pH meter.
Results of investigation are on the table 3
Table 3
The influence of lime milk consumption on the effectiveness of wastewater treatment after processing by AVS
(ferromagnetic particles: steel, d=1,6 мм, l=16 мм, m=175 g, τ=3 с)
Residual content of harmful agent, mg/dm3
|
Lime milk consumption (CaO) from theoretical calculation, % |
70 |
80 |
90 |
100 |
110 |
120
|
Fluorine content (F)
|
98,0 |
60,0 |
35,0 |
20,0 |
10,0 |
0,75 |
Phosphates content (P2O5) |
1290,0 |
750,0 |
8,4 |
0 |
0 |
0
|
Table 4
The influence of the processing by AVS on the effectiveness of wastewater treatment
Base values
|
Wastewater’s values after processing on AVS unit |
Wastewater |
Lime milk
|
pH
|
F, mg/dm3 |
P2O5, mg/dm3 |
CaO,% |
pH |
F, mg/dm3 |
P2O5, mg/dm3 |
3,65 |
350 |
2100 |
105 |
7,6 |
10 |
32
|
3,65
|
700 |
2250 |
105 |
8,2 |
7,5 |
8 |
5,9 |
1100 |
3200 |
105 |
9,2 |
5 |
0
|
3,0
|
1500 |
6500 |
105 |
11,5 |
1,2 |
0 |
3,0 |
1500 |
5100 |
110 |
11,6 |
1,15 |
0
|
3,95
|
750 |
5000 |
110 |
9,3 |
4,5 |
0 |
3,95 |
750 |
5050 |
110 |
8,6 |
7,1 |
0
|
3,95
|
750 |
5050 |
110 |
10,0 |
1,4 |
0
|
It was observed that application of AVS unit for fluorine-containing wastewater treatment is more effective than current used equipment.
The productivity of AVS-100 unit is 15 m3/h, AVS-150 – up to 40 m3/h.
For reference, by using traditional methods of treatment from fluorine, neutralization process lasts 1-1.5 hours. Residual fluorine content in the water is 50-60 mg/l. Even if we will be using the chain of reactors, relative productivity cannot exceed 0.25 m3/h. As you can see – the effectiveness of AVS unit is obvious.
Besides, defluorination and insolubilizing of fluorine passes in one stage. Treated water contains 1.5 mg/dm3 of fluorine and there are no phosphates. Processing time of wastewater treatment in AVS unit is 1-3 seconds. It is rational to use the lime as a reagent.
Installation of the AVS-100 unit enables one to provide a treatment quality below the maximum permissible concentration, reduces the consumption of reagent by 1.5-2 times, the consumption of energy by 2 times, reduces the working area by 10-15%, which results in high economic benefits.
Nitrocompounds in wastewater
AVS unit can be also implemented for water treatment from aromatic nitrocompounds. Usage of AVS allows restore nitrocompounds to amines. For this process we can recommend ferromagnetic particles made from soft carbon steel and diameter 1-1.4 mm, l/d from 12 to 16 mm.